Southern Precision Tooling Factory Tour: Interview, Andy Welshan – Part II
Paul B. 10.03.23
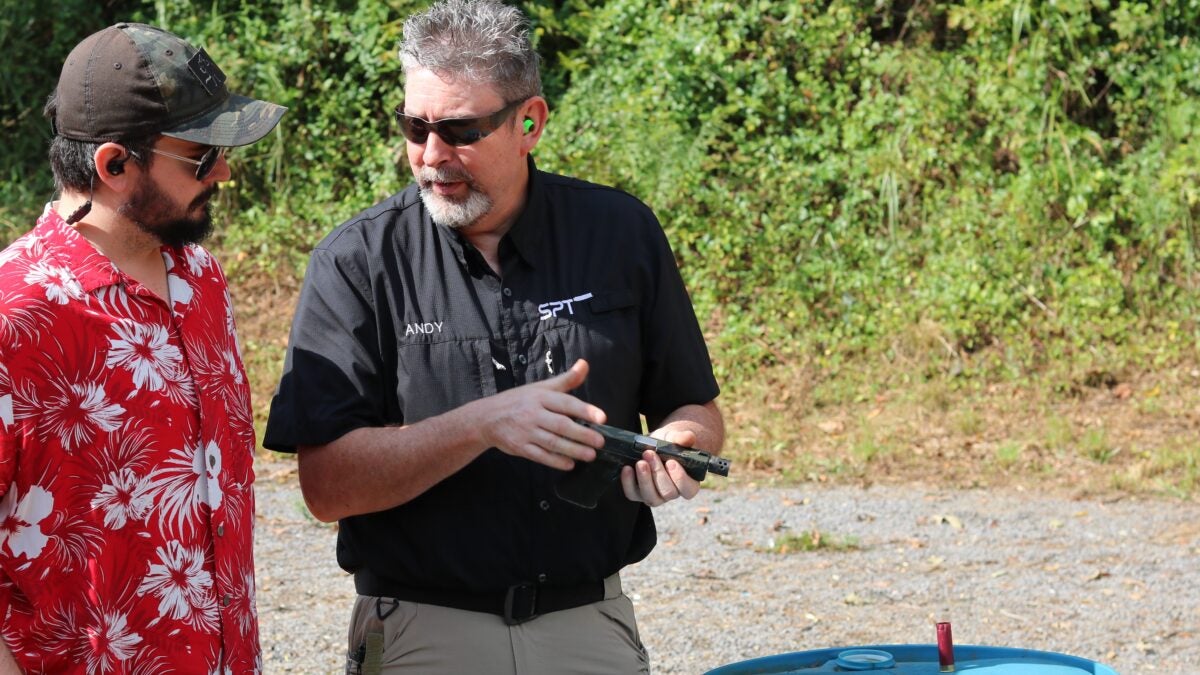
After our range day, I sat down with Andy and Norman of Southern Precision Tooling (SPT) to discuss the history of SPT and what they have planned for the future. Before we get into the interview, here are some links to check out Southern Precision Tooling, what they have to offer, and a list of events they will be at so you can check out some of their products for yourself. Take a look at their YouTube page to see some of their HU-DU brakes in action.
- Southern Precision Tooling Website
- Southern Precision Tooling on Instagram
- Southern Precision Tooling on Optics Planet
- Southern Precision Tooling YouTube
- Events: NRA 2024, SHOT Show, Memorial Three Gun Championship, Noddy After Dark, and possibly next year’s Triggercon.
Andy Welshan – Okay, a little history about Southern Precision Tooling. We started as a general machine shop. Norman (Owner) was doing contract work for probably 13 different factories. NAFTA showed up, all 13 went overseas, and we had nothing to do.
Paul B. – That unfortunately seems to be a common thing.
Andy Welshan – We decided that since me and Norman have worked on guns our whole lives that we would start doing some gunsmithing. So, some questions about the legality of us working on stuff for police departments came to the point that we went ahead and got a class three SOT.
Paul B. – What year was that?
Andy Welshan – We got the SOT probably two years after we started. Yeah 2009, 2010.
Paul B. – How does the HU-DU come about?
Andy Welshan – We had a gun customer who was an elderly gentleman who kept buying everybody’s muzzle brake to install on his guns because the recoil really bothered him. He had been putting them on and getting extremely underwhelming results. The guy was spending all this money for nothing.
So, in the middle of the night, Mr. Norman woke up from a dream, drew the HU-DU out on a pad that he keeps next to his bed, went back to bed, came in and said, I know what it’s supposed to look like.
So, we did the Edison thing, we made a prototype. We stuck it on a .300 Weatherby Magnum, our first cartridge that we tried. Got technical. We went to the roller door and we put duct tape on it and made us a grid pattern and set out here with a camera phone and recorded our results.
When we pulled the trigger on this thing, it was one of those OMG moments. We knew that we had something unlike anything on planet Earth. So, the first time we pulled the trigger, the gun went back about 10 and a half inches and up about 11 or 12. So, we screw the brake on and pull the trigger. The barrel went down two inches and back one inch. Norman did a little tweaking.
Added some holes to stabilize it out and what we did is we got in there and we pulled the trigger it didn’t go up, it didn’t go down, and came back a half inch so on our first try we took, due to our measurements, about 90% out of the recoil, turns out it was actually 87% after we finally got the testing done. Then, we brought in old gun guys “come over we want you to see something” and they pull the trigger and they’re like “oh no there’s no way.” We started the arduous process of patenting this thing and writing our own patent, which is a chore unto itself, but we got our own patent got it registered, got four other iterations of it including some bigger stuff and maybe something that we can eventually use with muzzle loaders we’re still trying to get a good .50 caliber muzzle loader brake so the guys there would love us
Paul B. – That would be interesting. It must be difficult to do something like that for a muzzle loader.
Andy Welshan – We’ve been talking about it, we’re so busy with getting everything else that we can’t stop for R&D, but we think we’ve got a pretty good idea in our head how to do a 12 -gage shotgun brake and take the recoil out of a 12 gauge.
Paul B. – So let me back up just a little bit. The first prototype HU-DU, what year was that one?
Andy Welshan – About seven years ago. It took us probably two years to get the patent and then after that we’ve got what we’re up to six now. So, we’ve got six separate patents on this. We’re covered on it. We started trying to figure out a name for this thing and we were gonna say, okay, we’ve got rocket engines on the end of the thing, we’re gonna call it the rocket brake.
Paul B. – Not a bad name. Any other names get considered?
Andy Welshan – Yeah, we said, OK, it voids out the recall, we’ll call it the void brake. Not bad. So, one of the brakes that we did in the early days, I’m talking the first few months that we’re really selling these things to was to a friend of mine. Now, he’s not just a regular Cajun, he’s deep swamp where they’ve got alligator DNA. So, we built him one for his 7mm Rem Mag.
I’m sitting here about a week after we made it and he went off to do his hunting trip and he comes in and launches his rifle into the middle of the table. Boom. And it just lands. I’m like, dude, what’s wrong?
And he looked at me said, What kind of hoodoo are you putting in my gun to make it do that? And so, HU-DU was born at that moment.
Andy Welshan – That’s where the name came from. We’ve been working to have a fast way to manufacture. We have got it down to where we’re using some modern technology. We’re using stuff that we learned during World War II about stage work to where we can really churn these out and with a very small crew, we can churn out quite a few brakes. We are gaining traction every day. Again, our number one problem is non -belief.
Paul B. – When we first talked. I didn’t believe it.
Andy Welshan – I can understand. I would never ever believe in a hover car till I ride in one.
Paul B. – I’m not sure what’s more unbelievable, the muzzle brake or the suppressor that we just shot.
Andy Welshan – And so we started again, Edison people. (For the Suppressor) We went from a three-inch tube to a 12-inch tube, half inch at a time, and we’d screw one in and shoot it. And we’d put the cap in and put the next one and shoot it. About a six-inch tube was the octave. So we put it on there and then tried it with different baffle systems and found out that it really didn’t do a lot and only thing we’re adding is complication to the suppressor.
So, we tried it with just the end cap and nobody is happier about this than me because now we just eliminated all of the death points of the suppressor. All of the spacers that get stuck, all of the baffles that get stuck, carbon locking.
We have no blowback in your face even on full auto, on a 10 inch barrel full auto and it was still completely enjoyable. We discovered that it’s more about keeping the gas in the tube as long as possible but spreading the volume of the gas out.
Paul B. – It was one of biggest “Wow” moments I’ve had in the firearm’s industry.
Andy Welshan – We were looking at it after 10 minutes it was cold. After running full auto through it we’ve sat it over there 10 minutes it was cold, too. Stick it in your front pocket.
Norman Griffitts – But look at it, look at it. There’s nothing there. So, yes, there’s something there. It’s called air.
Andy Welshan – We have the suppressor system if you have to go indoors drop the suppressor on it and everybody’s happy.
Make sure to watch for Part III of this series to read the completion of our interview with Andy Welshan, Plant Manager and Norman Griffitts, Owner. As always, let us know all of your thoughts on Southern Precision Tooling (SPT) in the Comments below! We always appreciate your feedback.